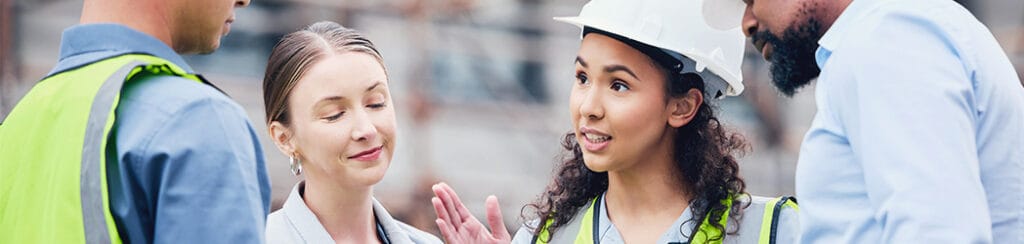
What happens when critical construction materials like wood, steel, or concrete are hard to find or even when their prices suddenly escalate? This is precisely the situation many contractors face today. Indeed, 93% of contractors report facing at least one material shortage, which substantially affects the industry. The shortages cause project delays, blow budgets, and leave teams struggling to get back on track.
With the right strategies, construction teams can overcome such obstacles and keep their projects moving. Let’s explore why material shortages happen and how to manage them effectively.
The Causes of Construction Material Shortages
Material shortages don’t happen by accident; they are caused by a combination of factors that disrupt the availability of essential supplies for construction projects. Knowing the causes helps in effective planning by construction teams and even reduces the impact such shortages may have on their work.
Supply Chain Disruptions
The primary cause of material shortages is breakdowns at various points in the supply chain. Steel, concrete, and lumber often travel long distances from factories, warehouses, and ports to construction sites. Any disruption—whether a delay at a port, a shortage of truck drivers, or a factory shutdown—can halt deliveries and create bottlenecks. These issues inevitably slow project timelines, leaving teams waiting for critical supplies.
High Demand Across the Industry
A surge in demand for construction materials can also lead to shortages. When numerous projects are underway at the same time, suppliers may struggle to meet the increased need. This often creates competition between contractors, driving up costs and lengthening wait times. Even teams that place orders early can face delays due to these industry-wide pressures.
Impact of Weather and Natural Disasters
Severe weather events and natural disasters further contribute to shortages. Hurricanes, floods, and snowstorms can damage supply routes, stop factory operations, and delay shipments. These events often paralyze entire regions, making it difficult for suppliers to maintain consistent deliveries.
Economic and Political Challenges
Economic and political factors also play a significant role. High tariffs on imported goods, trade disputes, and economic instability in manufacturing hubs can raise prices and restrict supply. For instance, a sudden increase in tariffs on imported steel can make the material both expensive and scarce, directly affecting project schedules and budgets.
Preventing the Project Critical Delay
When material shortages occur, they often lead to critical delays—where the absence of one essential item halts progress on the entire project. These delays are costly and frustrating, particularly for teams working under tight deadlines. Without the necessary materials, work may come to a standstill, leaving crews idle and budgets stretched thin.
In addition to causing immediate setbacks, poor material availability can disrupt planning and scheduling. Teams may need to pause one part of a project and shift their focus elsewhere, leading to inefficiencies and increased administrative burdens. This highlights the importance of preparedness and backup strategies to handle such challenges.
Improving Construction Material Delivery Reliability
Late deliveries can throw an entire project off schedule, so ensuring reliable material delivery is critical. Partnering with trustworthy suppliers with a history of good, on-time deliveries can make all the difference. Partner reliability reduces uncertainty and allows teams to plan with confidence.
Real-time tracking technology is another asset. It allows teams to monitor shipments and know exactly where materials are at any given time. If delays occur, this enables them to adjust their plans quickly. Clear and frequent communication with suppliers is also equally important; teams can help ensure deliveries meet their expectations by staying in touch and providing detailed instructions.
Managing Risks Linked to Supply Delays
No amount of good planning is foolproof, so delays should be managed well. One means of doing this is by holding a small stock of essential materials on-site as a reserve. This will ensure that work does not stop if the delivery of the items is delayed. Another option is to find substitute materials. This means that if there is a requirement for a particular type of steel, another material of a different grade may be used instead.
Cost planning is also essential. A contingency fund will be used to cover emergencies and balance all costs incurred while running the project. Another smart thing would be to change project schedules in case some materials for that part of the project are delayed since teams can work on other parts.
Overcoming Material Shortages with Smart Strategies
Shortages of construction materials represent a tough challenge, but they cannot be an excuse to derail a project outright. The causes can be understood, plans can be made ahead of time, and specific risks can be managed while staying flexible on the work to keep it on course. Building strong supplier relationships, using technology to forecast needs, or finding creative ways, such as substitutes and schedule adjustments, are just a few examples of what can be done.
How has your team coped with material shortages? Share your experiences and strategies in the comments below. Let’s learn from each other to build better and stronger teams, even in challenging times.