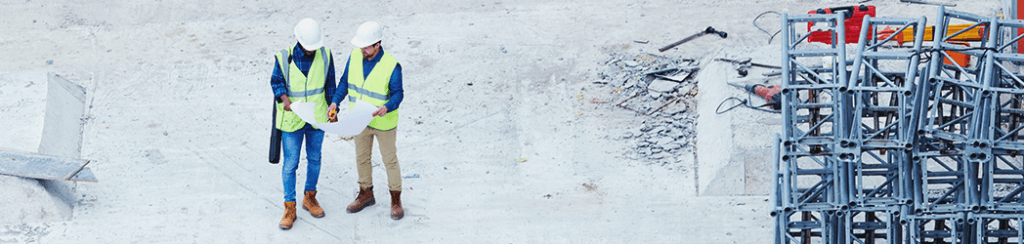
In construction, working efficiently is not just a benefit. It is a must for every project. Even small issues can quickly turn into big costs, long delays, and unhappy clients. Studies show that adjustments and disruptions, such as shortages of materials and information, can cause a 30% loss in labor efficiency on average. That kind of drop makes a big difference to your bottom line.
Here are five major construction inefficiency factors that often lead to lost time and money. You’ll also find simple ways to protect your construction budget and improve your construction documentation process.
The Most Common Construction Inefficiency Factors Impacting Teams
Every construction project faces challenges. To maintain productivity and achieve project success, construction managers and project stakeholders must identify factors that can affect overall efficiency. Lost productivity or inefficiency can stem from poor project planning, communication issues, or inadequate tools. These issues negatively affect actual productivity and lead to cost and time overruns.
Construction inefficiency factors often appear in small, unnoticed ways. They can affect how your team works, how people talk to each other, and how tools or paperwork are handled. Here are five issues that commonly slow things down:
1. Poor Planning and Scheduling
Without a clear and proactive project planning process, teams can quickly become overwhelmed. Delays in design and planning, overlooked details in the scope of work, or poor project controls can lead to missed deadlines, inefficient project execution, and added cost and time.
2. Labor Mismanagement
Skilled labor is essential to achieving planned productivity. When teams are poorly trained or not properly scheduled, it results in lost productivity and lower project performance. Project managers must monitor labor usage and address labor shortages quickly to maintain efficiency.
3. Ineffective Communication
A lack of clear communication between project stakeholders can disrupt collaboration and affect productivity. Misunderstandings lead to incorrect work performed, which causes rework, congestion on-site, and higher project costs.
4. Unreliable Equipment or Tools
Delays often happen when equipment breaks down or when the tools on hand are not fit for the job. This not only wastes equipment hours but also disrupts the critical path method schedule, causing a chain reaction of delays and overtime.
5. Inadequate Documentation
An outdated or unclear construction documentation process increases the risk of compliance issues and scheduling conflicts. Without proper project documentation, it becomes harder to assess performance, quantify delays, and maintain accurate project controls.
These construction inefficiency factors often connect with each other. For example, bad planning can lead to poor communication, which then leads to delays and documentation issues. Fixing one area often helps improve the others. That’s why reviewing your processes regularly can help you spot inefficiencies and fix them before they grow.
How Project Delays Create Cascading Operational Problems
Project delays cause more than just missed deadlines. These project delays can slow down your schedule, increase your costs, and hurt your team’s focus. They affect many parts of your operation. Here is a simple table to show how one delay can lead to bigger problems:
Delay Trigger | Immediate Impact | Cascading Effects |
Late material delivery | Workers waiting | Labor cost rises, schedule falls behind |
Poor weather planning | Tasks skipped or missed | Penalties, unhappy clients |
Subcontractor no-shows | Phase left incomplete | Cash flow slows down, other tasks delayed |
When project delays happen, your construction budget starts to stretch. Timelines shift, pressure builds up, and your team may have to rush. That’s why solving project delays early helps everything run better. The more you reduce project delays, the more smoothly your team can work from start to finish.
Protecting Your Construction Budget Through Process Optimization
Protecting your construction budget means making smart process choices. Without clear steps, projects can face delays, rework, and higher costs. These problems reduce productivity and hurt project performance. A consistent process helps project managers and construction managers stay on track, avoid risks, and improve efficiency.
Here are three simple ways to improve your process and protect your construction budget:
- Use Clear Workflows: Repeat steps that already work well. When everyone follows the same plan, mistakes are fewer and progress is faster.
- Track Key Numbers: Watch important numbers like labor hours and material costs. This helps you see problems before they grow.
- Use Real-Time Budget Tools: Digital tools can help you keep track of spending. They alert you when costs get too high, so you can fix them fast.
When you keep a close eye on your construction budget and improve how your team works, you spend less time fixing problems and more time finishing projects. These improvements also allow project managers to assess project performance and calculate productivity using reliable data like man-hours and equipment hours.
Streamlining Your Construction Documentation Process for Better Results
Streamlining your construction documentation process helps improve project performance and reduce delays. When teams can’t access clear, updated records, it leads to missed steps, confusion, and added risk. Errors in project documentation also make it harder to assess risks and calculate productivity, which affects delivery and raises costs.
Below are some common ways teams handle paperwork and how each method stacks up:
Paper-Based Documentation
Pros: Easy to use. Most people understand it.
Cons: Easy to lose, hard to share, and risky for compliance.
Email Approvals
Pros: Quick for one-time needs.
Cons: Easy to miss, hard to organize.
Cloud-Based Platforms
Pros: Keeps everything in one place, easy for teams to access, and good for teamwork.
Cons: Needs a little training to get started.
The construction documentation process should be simple and easy to manage. Using digital systems helps reduce mistakes, save time, and keep things organized. This makes it easier to pass inspections, protect your construction budget, and finish projects faster. It also improves teamwork and makes it easier to manage scope and risks.
Take Charge: Eliminate Inefficiencies and Reclaim Your Profits
We know how frustrating it is when simple problems end up costing a lot of time and money. Constructimize digs into the everyday issues that hurt construction teams the most, from unclear workflows to miscommunication and documentation delays.
By understanding what slows teams down, you can take steps toward smoother workflows, better planning, and stronger project outcomes, while also avoiding repeated project delays that impact both timelines and costs.
If you found this helpful and want more tips to improve your construction projects and protect your construction budget, check out other Constructimize blog posts.