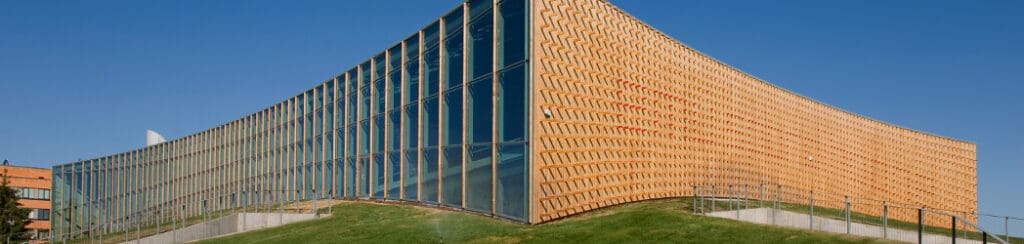
Choosing between standardization and customization is a common challenge for construction leaders. Each option offers trade-offs that can shape how smoothly a project runs. Striking the right balance is key to maintaining efficiency and achieving strong results. As part of the broader standardization vs customization conversation, it’s important to align your decision with your business needs, construction project timeline, and the right construction protocol.
Nearly 98% of large construction projects face cost overruns exceeding 30%, often due to poor estimates, scope changes, and payment delays. Making the right choice early can help avoid these issues and keep your project on track.
This blog breaks down the debate of standardization vs customization, helping you decide what approach works best based on goals, timelines, and the kind of work you do.
Understanding the Standardization vs Customization Debate in Construction
The debate between standardization and customization in the built environment boils down to predictability versus flexibility—two competing priorities that every project leader must carefully balance. Standardization refers to the use of consistent, repeatable processes across multiple projects. This method promotes uniformity, improves cost-efficiency, reduces training time, and allows for easier deployment at scale. On the flip side, customization allows builders to adapt processes to meet specific project needs, often enhancing client satisfaction through personalization and enabling design innovation.
While standardization is ideal for high-volume, repetitive builds that demand scalability and streamlined execution, custom construction is often better suited for complex, high-stakes projects with unique requirements. Understanding when and how to apply standardization vs customization can help project leaders strike the right balance, finding the optimal blend of consistency and flexibility to support both operational efficiency and customer experience. In the modern built environment, success often comes from combining the strengths of standardization and customization.
How Your Construction Project Timeline is Affected by Process Choices
Your choice between standardization and customization doesn’t just shape how your project is managed—it also directly affects how long it takes to complete. Process decisions have ripple effects on schedules, from planning through execution. Standardized processes often reduce project delays by streamlining steps and minimizing variables. Custom approaches, while more flexible, may introduce new dependencies that lengthen your timeline.
To better understand these impacts, here’s a simple cause-and-effect table:
Process Choice | Effect on Timeline | Why It Happens |
Standardized Process | Shortens timeline | Fewer decisions, faster procurement, reduced risk |
Custom Construction | May extend timeline | Extra design work, unique materials, complex tasks |
Hybrid Approach | Can optimize timeline with the right balance | Uses repeatable elements where possible |
The way you structure your project process has a direct impact on the construction project timeline. Standardization allows smoother coordination across teams, while custom construction needs more planning time but may offer better results for unique goals.
When to Implement a Standardized Construction Protocol
Standardization can be a powerful strategy, especially when repeatability, speed, and risk reduction are your top goals and when a consistent construction protocol aligns with your business model. A standardized construction protocol allows teams to follow consistent methods, which improves productivity and cuts down on errors. It’s ideal when your business depends on predictable performance, fast project delivery, or expanding across locations.
Not sure if standardization is right for your next project? Here are five signs it’s the smart move:
1. You Build Similar Structures Repeatedly
If your projects follow the same general layout or blueprint, standardization becomes a smart and scalable choice. By using a consistent construction protocol, you save valuable time, reduce design decisions, and avoid reinventing the wheel on each project.
2. You Need to Scale Across Teams or Locations
When your operations span multiple job sites or regions, maintaining consistency is key. Standardized processes help streamline training and ensure quality control, so that crews, no matter their location, follow the same steps and deliver uniform results.
3. You Want to Minimize Rework and Budget Overruns
In building projects, rework is costly. A standardized approach reduces uncertainty and supports better planning, which limits unexpected issues and helps stay within budget. With fewer on-site adjustments, you can deploy resources more efficiently.
4. You Aim for Fast Turnarounds
For projects that demand quick completion, speed is essential. Standardization streamlines procurement, scheduling, and execution, allowing you to move faster without sacrificing quality. Repeatable workflows shorten lead times and enhance operational efficiency.
5. You’re Focused on Reducing Project Risk
Managing multiple projects increases the risk of errors and delays. A well-established construction protocol helps reduce these risks by ensuring everyone knows what to do and when. It’s a dependable foundation that supports better project control and predictable outcomes.
If these apply to your work, adopting a standardized construction protocol could give your business a major edge.
When Custom Construction Approaches Deliver Better Results
While standardization fits routine projects, some jobs demand more flexibility and appropriate customization to meet individual needs and deliver personalized results. Custom construction is the right choice when you’re working with complex builds, unique site conditions, or clients who expect tailored solutions. These approaches give you more room to adapt, innovate, and create one-of-a-kind results, especially when a flexible construction protocol is required to meet project demands.
Let’s compare the pros and cons of using custom construction approaches:
Pros:
- Greater design flexibility for clients
- Better suited for unique or complex project needs
- Allows innovation with materials or layouts
Cons:
- Higher risk of delays
- More time needed for planning and coordination
- Often more expensive due to custom materials or one-off designs
Custom construction makes the most sense when your project requires tailored solutions or when client experience and aesthetics matter most, even if it means stretching your construction project timeline. While it can extend the construction project timeline, it may also offer results that stand out in value or function.
Smart Decisions for Stronger Builds
It can be challenging to find the right balance between structure and flexibility, especially when every project has its own demands. Constructimize shares practical insights into the decisions, trade-offs, and tools shaping construction projects today. Whether it’s standardization, customization, or anything in between, the goal is to help you think through complex topics with real-world context.
Making smart choices between these two paths can shape your construction project timeline, reduce risk, and lead to stronger project outcomes.
For more practical ideas on navigating key decisions in project planning, check out the other posts on Constructimize.